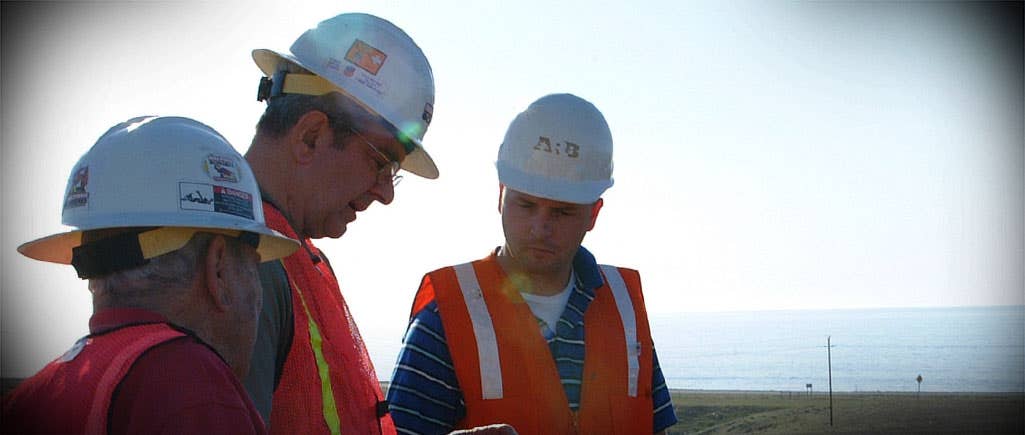
When it comes to selecting the right HDD tools for your job, the last thing you want to do is guess. Thereās too much on the line. So, when we get calls from drillers asking which Melfred Borzall tool to use, we always ask three important questions. Knowing these answers gives us a sense of the bigger picture, enabling us to provide the best information and suggestions for a successful drill.
-
What are the soil conditions?
We canāt give a recommendation about which type of blade or backreamer is best for a particular operation until we know what kind of soil youāre drilling ināand it can look a lot different below than on the surface. There are three main types of soil, and we recommend different HDD tools for each. Sandyā Sandy soil is the easiest to drill, from the standpoint of operating pressure. But sandy conditions require a good general-purpose blade with a lot of chunky hardfacing. Our UltraBit 3 is perfect for this, with plenty of carbide hardfacing for wear resistance. Itās also packed with aggressive conical carbide cutter blocks for chewing through tougher conditions, including sand-stone. Meanwhile, your reamer should be able to achieve maximum mixing and pumping action. Our Turbo reamer features curved packer blades, all ideal for sandy conditions. Clayā You might think of clay as being a doughy material, and it isāwhen itās wet. But underground, clay can dry out and compact into a fairly hard material. Therefore, you need a tool with a little more meat to it, something with more teeth. Our Tornado reamers are good examples because theyāve got carbide-tipped blades that are positioned to efficiently cut through hard compact materials, but still, retain excellent mixing and pumping action. Rocky ā Before deciding which bit or blade to use in ārockā, first determine if it is solid and hard (like granite), softer (like sandstone), fracturable (like shale), or cobbles. Each one might need to be attacked differently. For solid and hard rock, youāll need a mud motor or air hammer and a tricone or PDC bit. For reaming, youāll need to use a hole opener. (We carry a lot of these tools but if we donāt offer it, weāll tell you what you need and where to find it.) For softer rock and cobbles, youāll want something very stout with lots of thick, carbide cutters. Possibly a tool like our Ogre or Juggernaut, but with dome style carbide cutters for a better grinding action. Rock that fractures also needs to be attacked by a lot of carbide cutters, but these should have a conical or shark-tooth profile to break up the rock into small bits. Bits like the Steep Taper Ultra Bit and Eagle Claw are a perfect weapon to go up against conditions like shale and caliche.
-
What are your job conditions?
Your conditions include things like type and diameter of the product pipe youāre installing, the profile of your bore and the distance of your shot. For basic straight shots, youāll need to know the maximum outer diameter of your pipe, then multiply by 1.5 to determine the size of backreamer you should use. We need to know more about the bore profileĀ (How deep? How long is the bore? Are there any drastic bends?) so we can make sure that your hole will have sufficient diameter to handle the drill string and product pipe without squeezing or stretching the pipe, or causing road humps. Remember: the longer your bore, the more critical it is that you stick to that 1.5x multiplier.
-
What drill rig are you using?
Your rigās make, model, and size tell us right way the range of tools that are designed to fit your machine. In particular, knowing the size of your rig is especially important so we can recommend the right combination of tooling, including blades, reamers, and swivels. We need to ensure that the reamer matches your rigās power rating. You donāt want a reamer on a shaft that isnāt rated to handle the torque or pullback of your rig. We also need to ensure the threads and blade bolt-pattern match your OEM connections. Knowing your rigās model number will also give us information on the drill fluid flow that is available. This will also be important when recommending particular HDD tools or the specific process for completing the bore successfully. On a side note, if yours is an uncommon rig or you need a custom HDD tooling solution, we can engineer a custom adapter to connect pretty much any tool to any rig. An HDD distributor who asks lots of questions is a distributor who cares about your jobās success. The more information you can supply, the better. Having the answers to the above questions ready when you call will help you order the right tool so you can make sure your job gets done right.